Micro resistance welding of copper and copper | Explaining how to reduce spatter in resistance welding
- TOP
- Resistance Welding
- Applications of Resistance Welding
- Micro resistance welding of copper and copper | Explaining how to reduce spatter in resistance welding
Is it difficult to weld copper?
Breakers and relays are used as components that interrupt the current, such as in switchboards and electric vehicles.
In breakers and relays, copper-based materials are used for components such as contact points and coils, and they are joined using resistance welding.
“How can we reduce spatter?”
“We want to weld without discoloration. How can we achieve it?”
“I want to make the height consistent after welding, but I don't know how to do it.”
Due to the challenging nature of welding copper given its properties, do you have any concerns like these?
In this article, we will introduce the reasons why welding copper is difficult, as well as the differences in welding quality between AC welder and inverter welder
Why is it difficult to weld copper by micro resistance welding?
Welding copper is considered to be challenging because of its material properties.
3 Properties of Copper
Copper is a material with exceptionally low electrical resistivity compared to other metals.
Copper and copper alloys are mainly used in products that conduct electric current, such as electric wires, motors, and breakers.
Here are three properties of copper.
- Low electrical resistivity
- High thermal conductivity
- Low softening temperature
1.Low electrical resistivity
In resistance welding, which utilizes heat generated from the material, low electrical resistivity makes it difficult to weld because the material does not easily heat up when electric current is applied.
2.High thermal conductivity
Copper is also a material with extremely high thermal conductivity.
The thermal conductivity of copper is approximately six times greater than that of iron and three times greater than that of aluminum.
In resistance welding, the high thermal conductivity of a material means that the heat at the welding point is quickly dispersed and not retained, making the welding process more challenging.
Because the heat at the welding point rapidly dissipates, it takes longer to raise copper to the temperature needed for welding.
3.Low softening temperature
The melting point of copper is relatively high among metals, at 1084.5 degrees Celsius, but it becomes soft around 200-300 degrees Celsius, so care must be taken to avoid deformation.
The heat generated during resistance welding causes the copper to deform rapidly during the welding process.
Three tips for achieving a clean micro resistance weld with copper
How can copper be welded without spatter or discoloration, and with consistent deformation after welding?
Considering the characteristics of copper, it is necessary to weld by paying attention to the following three points.
- Rapidly raise the temperature to the required welding temperature.
- Maintain vertical pressure during welding to ensure consistent workpiece deformation.
- Control the current and height according to variations in welding conditions.
How to weld copper with a resistance welder?
Proper selection of welding power supply, electrodes, and weld head is essential to achieve clean welding of copper by resistance welding.
What is the procedure for welding copper using a resistance welder?
In resistance welding, the object to be welded (workpiece) is sandwiched between the upper and lower electrodes and pressurized, current flows through the electrodes to the workpiece, and the welding point is melted by the resistance heat generated between the object and the electrodes.
Since it is a contact-based welding method performed under pressure, it provides more stable welding conditions compared to non-contact methods such as laser welding.
On the other hand, non-contact welding methods such as laser and TIG welding exhibit variations in heat transfer and heat spread during welding due to inconsistencies in the materials being welded.
Consequently, it is claimed that the results of such welding processes are less consistent than resistance welding.
Selection of electrode materials and electrodes for resistance welding
Advantages and disadvantages of copper-based alloy electrodes
There are generally two types of materials used for the electrodes in resistance welding, which clamp the workpiece and pass current through it.
Copper alloys such as “copper chrome” and “copper beryllium” and materials such as “tungsten” and “molybdenum” that generate heat at the electrode itself.
Additionally, the selection of electrode materials is made considering the "heat balance" based on the material of the object being welded.
The term "heat balance" of electrodes describes the balance between heat generation and dissipation in resistance welding.
This balance is a critical element that greatly influences the welding quality.
Advantages and disadvantages of electrodes based on materials that generate heat (tungsten, molybdenum)
Advantages
- High current efficiency.
- Excellent heat dissipation.
- Good machinability.
- Cost-effective.
Disadvantages
- Forms alloys with coatings such as Sn (tin), causing the workpiece and electrode to adhere easily.
- Susceptible to shape changes of the contact surface due to heat and wear.
- High maintenance frequency required .
Maintenance of resistance welding electrodes
The electrodes used in resistance welding wear and deformed over time at the contact surface.
Due to deformation, changes in the contact area with the workpiece, as well as variations in heat generation and dissipation during welding, can occur, leading to inconsistency in the welding results.
Regular maintenance of the electrodes is essential to minimize welding inconsistencies.
We also have a "copper-tungsten material" electrode that balances maintainability with the advantages of copper-based materials.
Challenges of tungsten electrodes in welding copper
Tungsten electrodes are used for welding copper.
When using electrodes made of copper-based materials, both the workpiece and the electrode will have high thermal conductivity, which makes it challenging to produce heat and difficult to weld.
Welding is performed using tungsten electrodes, which are heat-generating materials, to supply heat to the welding target.
However, there are also challenges with tungsten electrodes.
Tungsten electrodes, which produce a lot of heat, tend to accumulate heat, making it necessary to allow time for cooling before proceeding to the next weld.
If the electrode is not sufficiently cooled before the next welding, the residual heat in the electrode can cause variations in the electrode temperature at the start of welding.
Variations in electrode temperature significantly affect the welding results on the workpiece.
To weld copper, controlling the current with consideration of the temperature variations of the tungsten electrode is essential.
What is a weld head?
The weld head holds the upper and lower electrodes and exerts a consistent pressure on the workpiece (the object to be welded) while passing welding current through it.
By applying pressure to the workpiece and passing welding current, heat is produced between the contact surfaces.
Resistance welding operates on the principle of generating heat through the use of the base material resistance and contact resistance between the workpieces.
Challenges of Welding Heads in Copper Welding
The weld head uses a pressure mechanism with cylinders or springs, and the welding current starts once the set pressure is reached.
When welding soft materials like copper, it is essential to use a welding head designed to follow the deformation of the workpiece during welding.
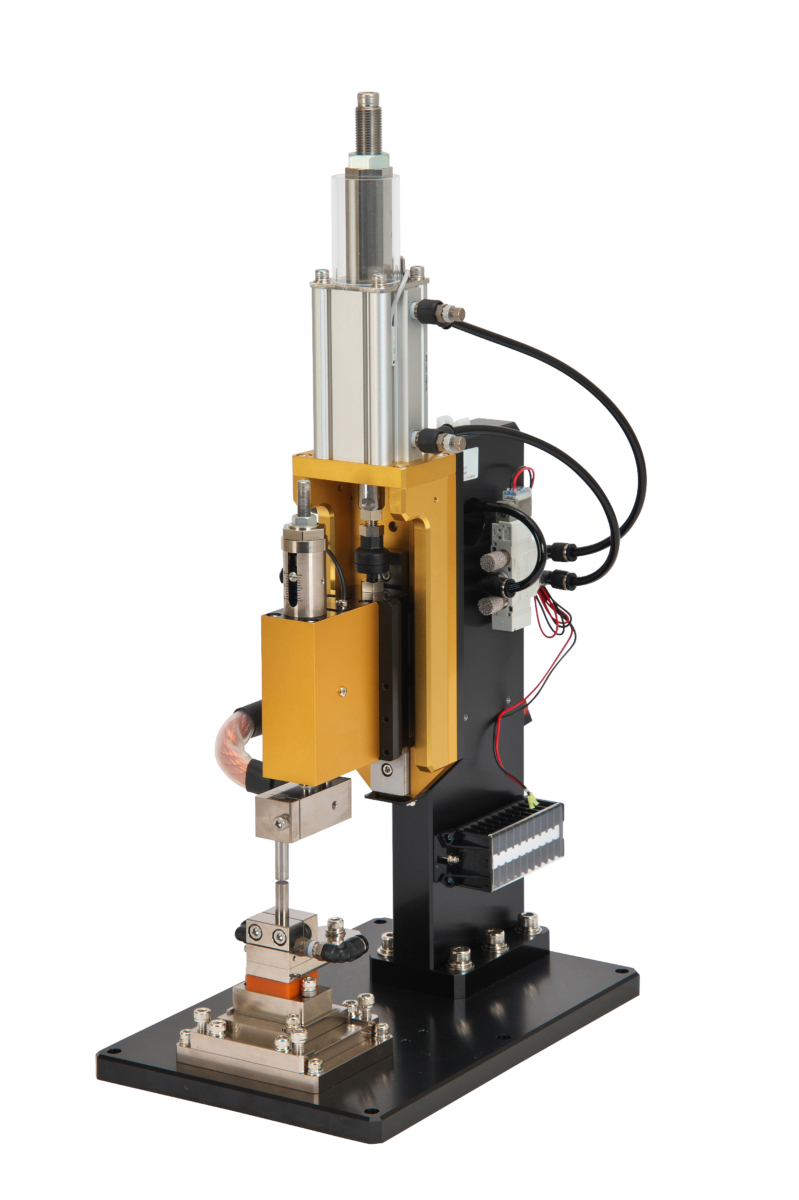
The principle of resistance welding is here.
Challenges of Welding Copper with AC Welding Power Supply
As previously mentioned, the following three points are important for welding copper cleanly.
- Rapidly raise the temperature to the welding point.
- Apply vertical pressure during welding to maintain consistent workpiece deformation.
- Control the current and height in response to changes in the welding conditions.
The traditional combination of "AC welder and shift-type heads" is unable to satisfy the three conditions necessary for the clean welding.
The challenges of AC welding power supply are
AC welding power supply use AC waveforms for welding, causing the welding current to alternate between positive and negative at a constant frequency, continuously switching ON and OFF during welding.
When switching from positive to negative, there are moments where no current is flowing.
During the OFF periods when no current is flowing, the necessary current for raising the workpiece temperature is not supplied, causing the temperature graph of the workpiece to rise in a zigzag pattern instead of a straight line.
Using an AC welder in this way causes inefficiencies in raising the workpiece temperature, prolonging the time required to attain the necessary welding temperature.
As a result, the thermal effect on the workpiece increases, causing issues such as:
- Workpiece discoloration
- Increased deformation of the workpiece
- Increased wear of the electrodes
Furthermore, products like AC welder is referred to as open-loop systems, which merely output the pre-set welding conditions as they are.
Since there is no corrective function to adapt to changes such as the state of the workpiece or electrode heating, it cannot cempensate efefect of disturbances.
On the other hand, products like inverter welders with feedback functions during welding are referred to as closed-loop systems.
To overcome the challenges of AC welders
To overcome the challenges of AC welders, the following four points are necessary:
- The ability to supply a welding current that may raise the workpiece temperature linearly in a short time.
- During mass production, the starting temperature of the electrodes can vary,thus, the system should have the capability to automatically adjust via feedback during the welding process (closed-loop control).
- The ability to automatically adjust welding conditions for each shot to ensure consistent heating during welding.
- The ability to detect displacement values and end the welding process to ensure a consistent finishing height of the workpiece.
Leave it to Nippon Avionics to solve your copper welding challenges!
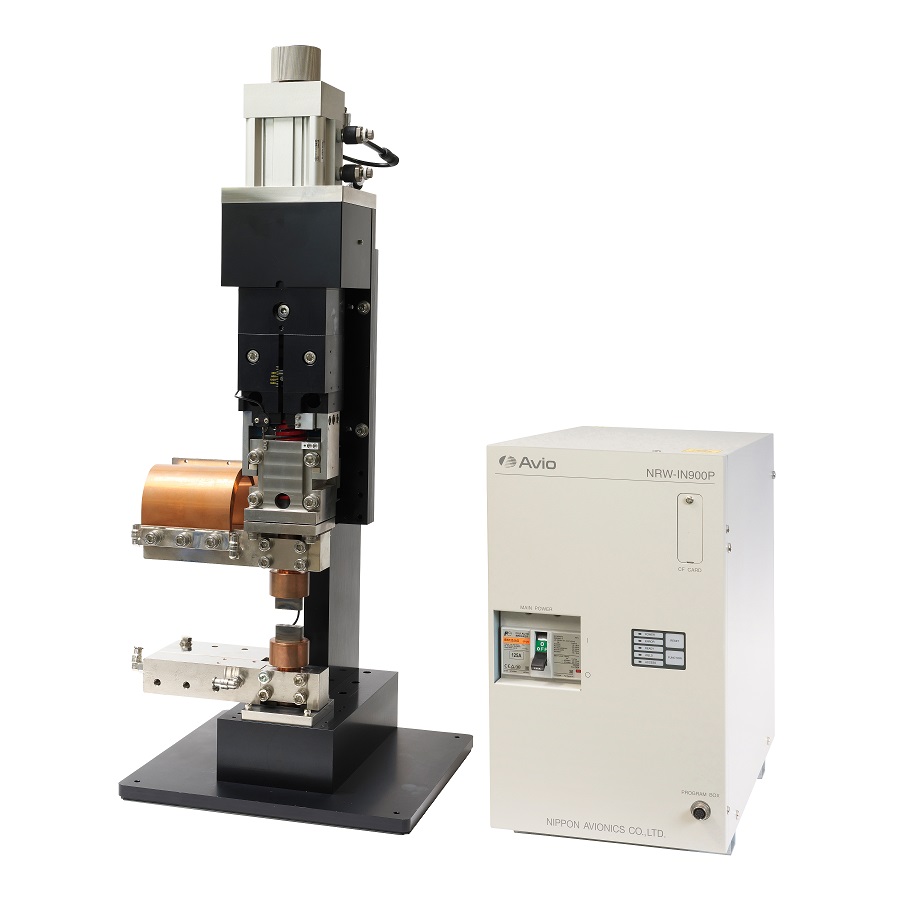
The high-reliability inverter welder "NRW-IN400PA and IN900P" from Nippon Avionics are resistance welding power supply designed to solve challenges of copper welding.
The inverter welders use closed-loop control to feedback the behavior of the copper's resistance during welding and adjust the current accordingly.
Specifically, among inverter welders, the "High-Reliability Inverter Welder NRW-IN400PA and IN 900P" utilize a higher frequency of 5kHz compared to other companies, enabling precise current control in the frequency band that ensures clean copper welding.
The high frequency allows for a linear increase in the workpiece temperature, achieving short welding times.
By utilizing a 5kHz frequency, the ripple is minimized, allowing for reduced spatter during welding compared to conventional inverters with lower frequencies.
The ability to control welding conditions in real-time, combined with external sensors, ensures a consistent finishing height for soft copper welding.
Key Features of High-Reliability Inverter Welder
- 5kHz frequency control to minimize ripple and suppress spatter
- Phase skip function that monitors current and voltage to stop power supply, reducing thermal damage to workpieces and electrodes
- Peak limit control function that manages voltage rise as resistance increases during copper deformation, preventing over-melting
- Feedback shift function that monitors current and voltage to skip power supply phases, reducing thermal damage to workpieces and electrodes
- Welding condition correction function that fine-tunes the welding waveform target value based on external signals, ensuring optimal welding
in response to changes in room temperature and electrode temperature.
"High-Rigidity Weld Head NB Series" by Nippon Avionics, suitable for copper welding
For copper welding, where shape changes easily occur due to applied pressure during welding.
It is difficult to maintain a constant inter-workpiece resistance value with a shift head that has a large second moment of area.
Therefore, it is necessary to apply pressure using a high-rigidity, vertical direct pressure weld head structure.
The "High-Rigidity Head NB Series" by Nippon Avionics solves deflection during welding through its high-rigidity twin-shaft structure.
Even for copper with large displacement, stable pressure can be applied every time, ensuring consistent welding with minimal variation.
Key Features of the High-Rigidity NB Series
- Enhanced rigidity through twin shafts
- High rigidity owing to direct mount design
- Employs a replaceable electrode holder, allowing for one-touch electrode changes
- Load cell can be built-in without any modification
- Displacement sensor can be built-in without any modification
- Supports various presure range with spring replacements
Avio‘s “High-Functionality Welding Monitor QC-450” is Ideal for Quality Control in Copper Welding
Copper welding is commonly utilized in components that serve as current paths, making it necessary to guarantee welding quality through post-weld quality control.
QC-450 monitors various parameters during welding and performs pass fail evaluations.
In copper welding, it is particularly important to manage the sinking amount of the workpiece due to thermal effects.
Therefore, the values from the load cell for load and the displacement sensor for displacement are crucial from a quality control perspective.
Examples of Copper Welding Applications in Breakers and Relays
There are many coppers welding in breakers and relays.
Here are types of copper welding applicable to our highly reliable inverter-type welder.
Application examples for breaker
Parts | Method | Applicable Model |
---|---|---|
Braided Wire | Compacting | NRW-IN400PA |
Braided Structure x Terminal | Resistance Welding | |
Coil Wire x Terminal | Resistance Brazing | |
Braided Wire x Bimetal | Resistance Welding | |
Oil Dash Pot(Oil Dash Pot) | Can Sealing | NRW-IN900P×2 |
Application examples for relay
Parts | Method | Applicable Model |
---|---|---|
Contact x Terminal | Brazing | NRW-IN400PA |
Braided Wire | Compacting | |
Braided Wire x Terminal | Resistance Welding | |
Nichrome Wire x Terminal | Resistance Welding | |
Coil Wire x Terminal | Fusing | |
Stranded Wire x Terminal | Resistance Welding |
Welding Example
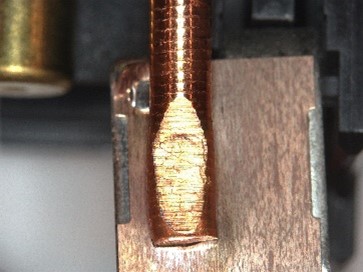
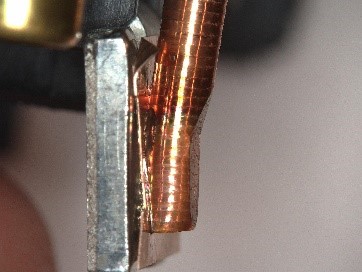
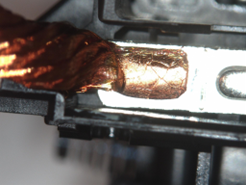
Coil Wire x Terminal
Braided Wire x Terminal
Having issues with copper resistance welding? We can help improve your results.
Copper welding is considered to be challenging, but selecting a resistance welder that meets the three essential factors required for copper resistance welding can resolve these issues.
Three Key Factors for Clean Copper Welding:
- Quickly raising the temperature to the required welding level.
- Applying vertical pressure during welding to ensure consistent workpiece deformation.
- Controlling the current and height to adjust for changes in welding results.
Avio’s inverter welder, welding monitors, and high-rigidity heads offer the best support for copper welding in the industry.
We provide technical support for anyone who face challenges with their copper resistance welding.
Please feel free to contact us.
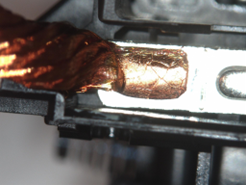
Joining Method | Resistance Welding |
---|---|
Processing Method | Metal Joining |
End Products | breaker relay |
Sample test
We will be pleased to test your sample with our proposed joining method, and return it with a report.
Related Link
Applications
Products
- Resistance Welder High-reliability Inverter Model NRW-IN900P
- Resistance Welder Inverter Model NRW-IN400PA
- Resistance Welding Monitor QC-450