How to join wires to a circuit board without removing the coating from the wire
- TOP
- Resistance Welding
- Applications of Resistance Welding
- How to join wires to a circuit board without removing the coating from the wire
For motor coil terminal processing, heaters, RFID, noise filters, etc., enameled wire or magnet wire coated with an insulator is attached to a circuit board or metal terminal.
Typically, the coating is removed to expose the copper or aluminum material, and then soldering is performed.
One method to eliminate the coating removal process and increase work efficiency is to use a resistance welder to perform thermocompression bonding.
What are the challenges of coated wire soldering?
What is the coated wire?
Many people may be confused about the difference between coating and insulation.
Coating refers to the state in which a molten insulator is baked onto a wire such as copper or aluminum wire to cover it.
On the other hand, insulation refers to the state in which a wire is protected with vinyl or other materials.
A coated wire is a cable that has a metallic appearance on its surface, like enamel wire or magnet wire.
Challenges of soldering coated wires
To solder coated wires to a circuit board or metal terminal, it is necessary to remove the protective coating to expose the conductive wire underneath.
There are two methods to remove the coating, but there are challenges when it comes to mass production.
Challenges when chemically removing with a remover
- Due to capillary action, the remover may penetrate deep into the wire and cause product failure.
- Strict management is required for the storage and handling of chemicals.
Challenges when removing by soldering
- In the case of high-temperature resistant coatings, there are challenges such as copper corrosion and a shortened lifespan of the soldering bath.
How to join to the board without removing the coating
By thermocompression bonding using the resistance welder, it is possible to achieve joining without removing the coating and without the use of solder.
How to join coated wires without soldering
What is thermocompression bonding of coated wires using resistance welding?
Generally speaking, when you think of resistance welding, you probably think of joining metal to metal.
Resistance welding is a method in which a high current is passed through the material to be joined, heating it through the generation of "Joule heat".
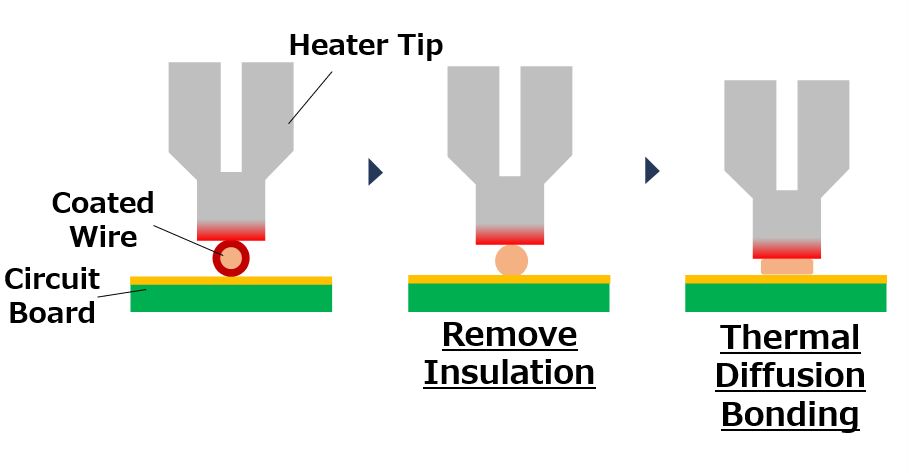
When joining a coated wire with a resistance welder, use a heater tip-shaped electrode like our Pulse Heat, which is used for soldering.
By flowing electric current through the electrodes, heat is generated to melt the coating and achieve the compression bonding.
The process of using heated electrodes in resistance welding to create a bond is known as heat diffusion bonding.
What is diffusion bonding?
Diffusion bonding is a method of joining materials by applying pressure to bring them into close contact and achieving a metal bond between the mating surfaces, while minimizing plastic deformation as much as possible, under temperature conditions below the melting point of the base material.
When joining coated wire, the coating is melted using the heat from the electrodes generated by a resistance welder, exposing a new surface of the wire, and the wire is then pressurized to create a diffusion bond (solid-state bond).
Four advantages of joining coated wires by resistance welding
By joining with a resistance welder, it is possible to improve production tact time and shorten the manufacturing process.
- The required joining time is approximately 0.02 seconds, resulting in a faster production cycle time.
- Because there is little heat effect on areas other than the joint, there is less heat effect on surrounding parts.
- The coating removal process is eliminated which result in shortened manufacturing process.
- It allows for reduced management workload and cost savings associated with the handling of chemicals and other materials.
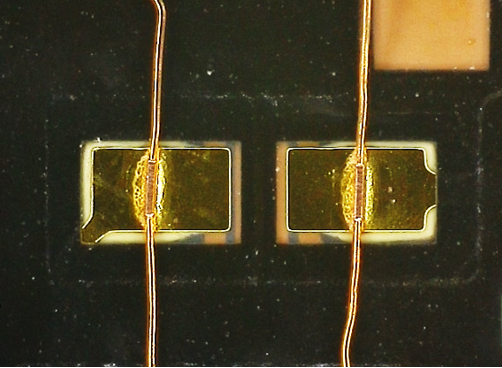
Resistance welding is the optimal method for joining solderless coated wires when a large quantity needs to be produced in a short amount of time.
Inverter type resistance welder NRW-IN400PA
The inverter type resistance welder NRW-IN400 PA is a resistance welding machine that can join wires without removing the coating and without soldering.
Due to its high frequency of 5kHz, the current can be rapidly ramped up, allowing for shorter intervals between joint.
In addition, by allowing for customizable waveform control settings, it can achieve precise heating that is suitable for the size of the heater chip.
Moreover, the use of a multi-transformer system that can handle four joining processes with a single power supply allows for cost reduction in terms of the initial investment when introducing a resistance welder.
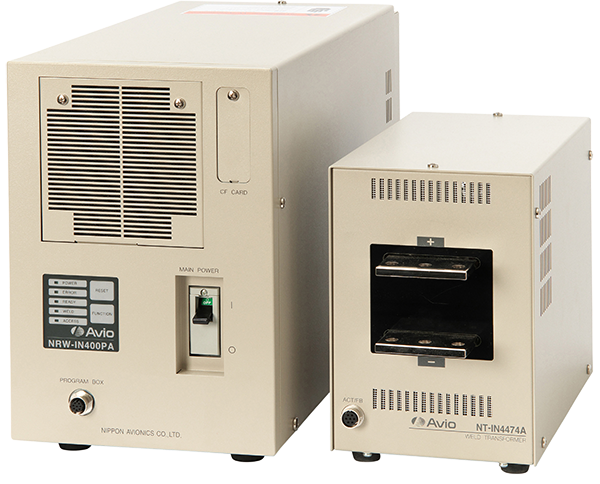
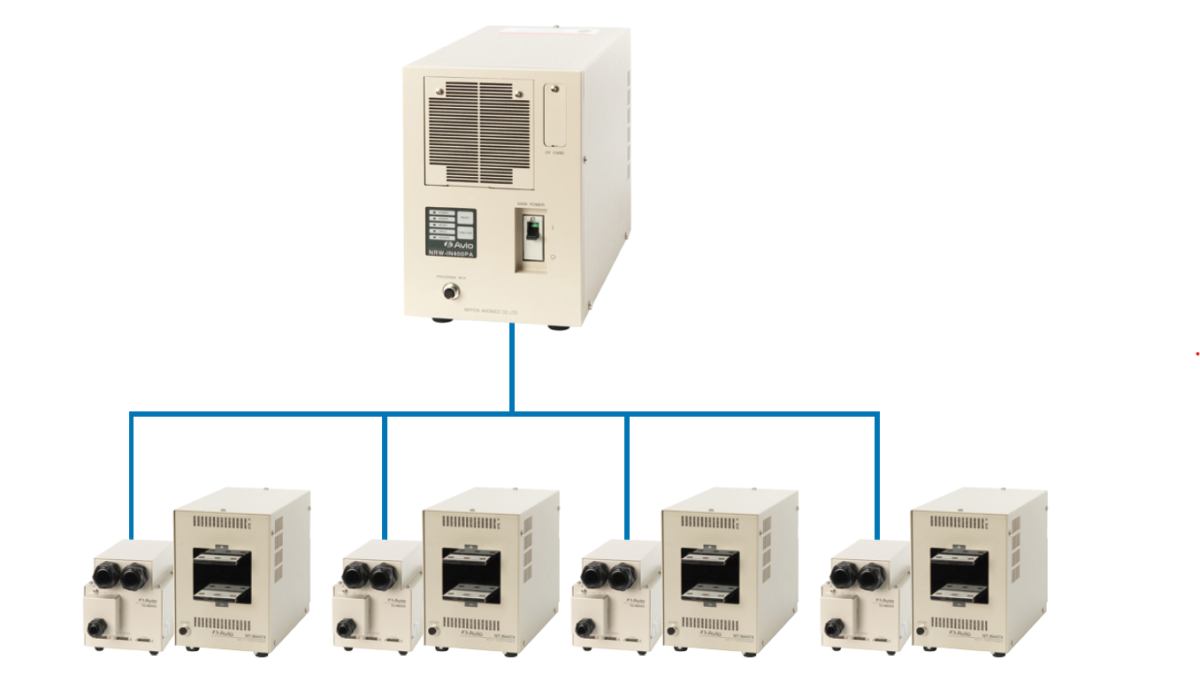
Click here for detailed product specifications.
Removing the coating is the challenge when joining a coated wire to a board.
The inverter resistance welder NRW-IN400PA can remove the coating and connect the wire at the same time without using solder.
Moreover, it can be joined in a shorter time than soldering.
How about considering it for the purpose of shortening the cycle time and improving the process?
At Nippon Avionics, we are happy to accept process sample tests for you.
Please contact us.