Principle of Resistance Welding
- TOP
- Resistance Welding
- Principle of Resistance Welding
Resistance Welding is used for joining two metals.
Resistance Welding Machine is consists of a welding head, which holds the metal between its electrodes and applies pressure, and a welding power supply, which applies electric current to the metal to be welded.
Resistance Welding Model, Temperature Distribution at the Welding
Resistance generates friction heat when force is applied. Resistance welding utilizes this heat.
Similarly, when an electric current tries to move forward through two metals, heat is generated due to the resistance of the metal itself and the friction at the contact point.
Resistance welding welds a metal to another metal utilizing this heat and pressure.
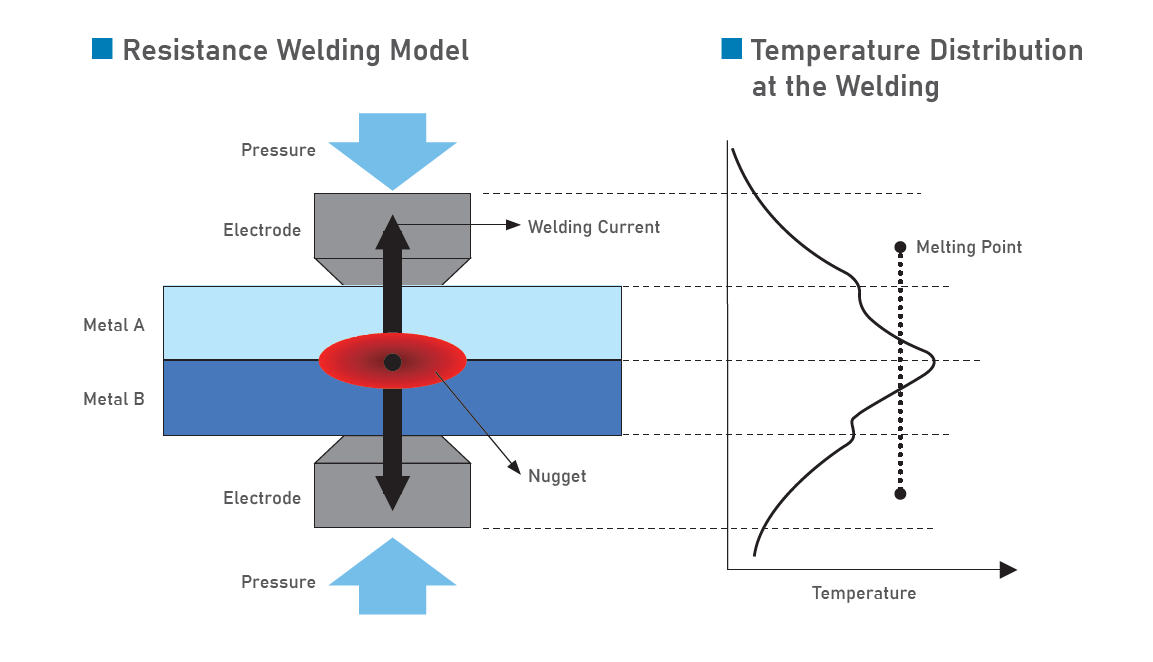
Basic Configuration of Resistance Welder and Role of Each Part
resistance welding machine sandwiches an object to be welded by the welding electrodes,
and applies electric current while applying a pressure.
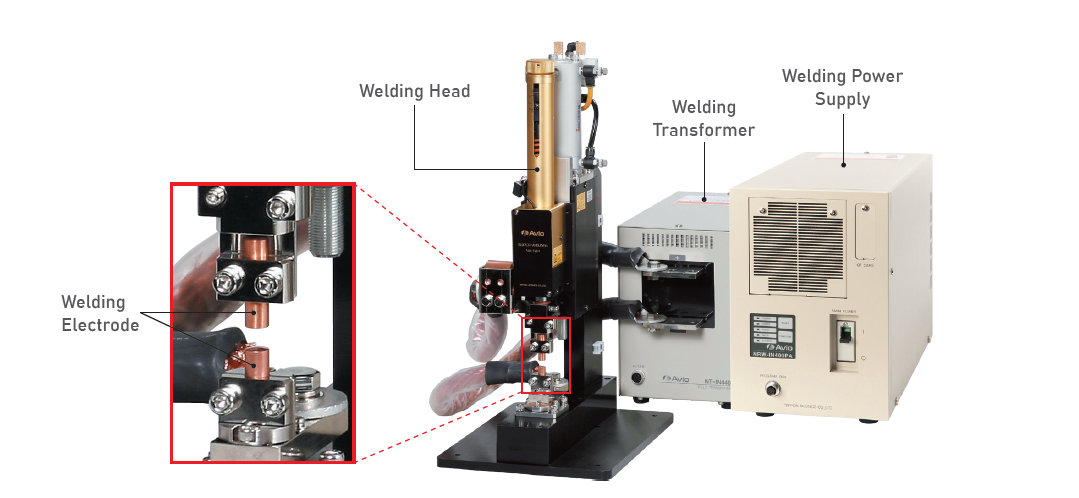
- Welding Power Supply: It controls the magnitude, time and waveform of electric current
- Welding Transformer: It converts the electric current from the power supply to a larger current
- Welding Head: It controls the pressure to be applied
- Welding Electrode: It contacts the object to be welded to apply pressure and electric current
*In addition to the above, we have various monitors which measure electric current or applied pressure.
Welding Power Supply: Control Method
An appropriate welding power supply must be selected based on the material or shape of the object to be welded and the required welding quality. There are three different types in our welding power supplies based on the type of control of the welding current, and each type is selected in a way to best demonstrate its characteristic in welding.
Basic System | Welding Current Wave Form | Feature |
---|---|---|
Inverter Type![]() | ![]() | The current is controlled in a cycle of several kHz (milliseconds) using an inverter circuit. Avio inverter type welding power supply is suitable for precision welding becuase it is DC type with good thermal efficiency and has a fast control cycle.. Stable welding quality is achieved by current and voltage feedback control. Since the capacitor is not charged, welding time can be set longer (up to 3 seconds *), and flexiblity of welding waveform setting is high. * When welding time is set long, restrictions are applied for the maximum current value and the duty cycle. |
Transistor Type![]() | ![]() | The electricity charged in the capacitor is directly controlled by the transistor. Since the control speed is extremely fast, every 0.01 milliseconds, it is suitable for ultra-precision welding of very small components and ultrafine wires. Stable welding quality can be obtained by current and voltage feedback control. |
Capacitor(DC)Type![]() | ![]() | It controls the electricity (energy) charged in the capacitor, and releases the charged electricity all at once for welding. Since a large current can be applied in a short time (several milliseconds), it is used for welding materials such as aluminum and copper that have high heat diffsapation and difficult to weld. It is also used for welding small parts that need to avoid heat infulence by taking advantage of a large current-short time welding capablity. |
Welding Head & Electrode
How to contact electrodes (how to apply welding current) is determined according to the shape and structure of the welding object. In addition, the shape and material of the electrodes and the value of pressure force are also important factors for the resistance welding.
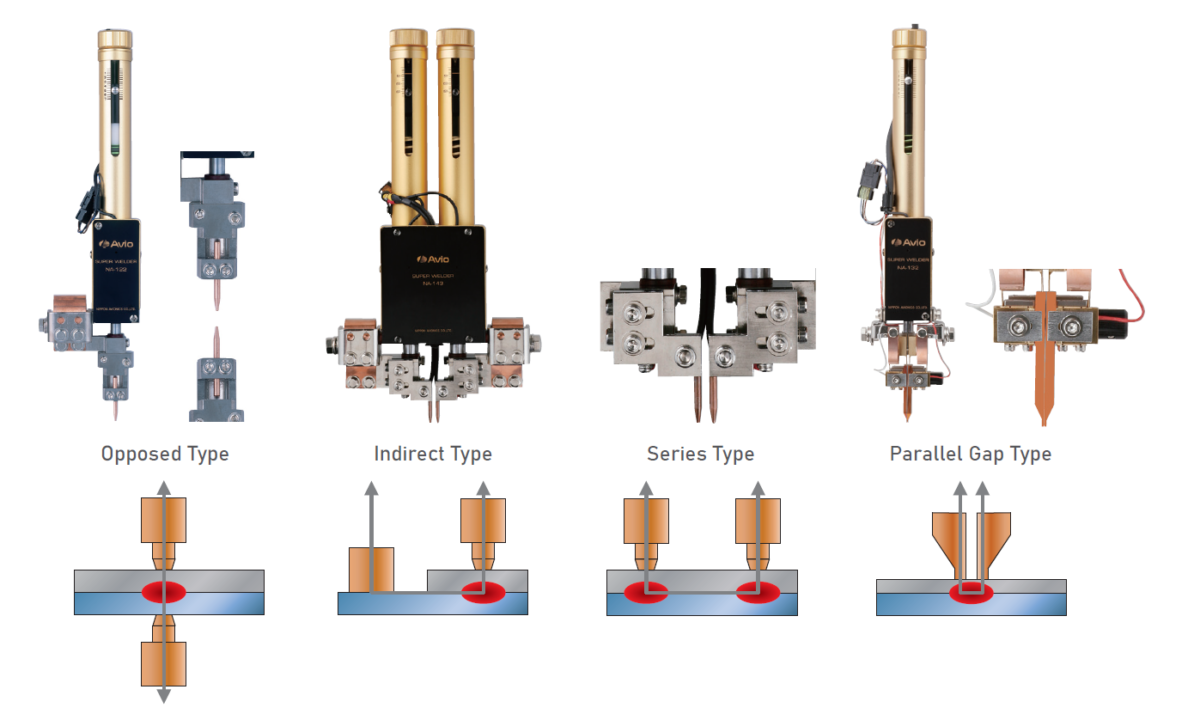
Movie Introducing the Principle of Resistance Welding
Please be careful about the volume adjustment as this movie contains sound.