Pulse Heat case study | Soldering of high heat dissipation boards such as ceramic boards by pulse heat
- TOP
- Pulse Heat (Hot Bar Reflow) Soldering
- Applications of Pulse Heat (Hot Bar Reflow) Soldering
- Pulse Heat case study | Soldering of high heat dissipation boards such as ceramic boards by pulse heat
Substrates made of ceramic, aluminum, copper, etc. with excellent heat resistance and high heat dissipation are used for infrared sensors, ultrasonic sensors, LED lighting, etc.
Because ceramic, aluminum, and copper have excellent thermal radiation properties, substrates made of those materials are hard to warm up and difficult to solder components on them.
Pulse heat with the top-to-bottom heating technique is an easy way that ensures stable strength of soldering.
What is high heat-dissipating board ?
A high heat-dissipating board is a substrate with good heat dissipation, and materials such as ceramic, aluminum, and copper are commonly used.
Components in electronic circuits generate heat due to the internal resistance when current is applied.
The generated heat can cause deteriorated performance and reduced life of the device.
Heat generated by the components is dissipated to the board, which results in suppressed temperature rise of the components.
Its applications include LED lighting and power device.
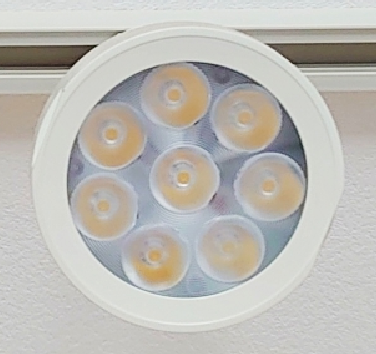
Challenges when soldering on the high heat-dissipating board
The high heat-dissipating board rapidly dissipate heat to the outside.
Solder does not melt easily because the temperature does not rise to that level when you try to solder the components on them.
There are two issues from the fact that the solder does not melt easily.
- Solder strength is not stable
- Components move out of their positions
The high-dissipating board is difficult to solder components on.
The problem of soldering the high-dissipating board can be solved by top and bottom heating with pulse heat, which can instantaneously heat and cool the board.
What is pulse heat soldering with top and bottom heating ?
The high heat-dissipating board, such as ceramic, can be steadily soldered by heating the board from bottom simultaneously.
The board is sandwiched from the top and bottom to keep the temperature of solder to melt, preventing heat from escape.
In addition, shorter cycle time is achieved by rapid heating from the board side of the high heat-dissipating board.
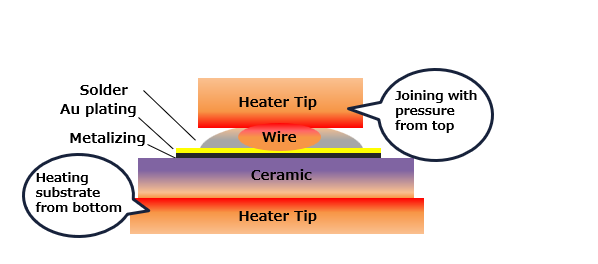
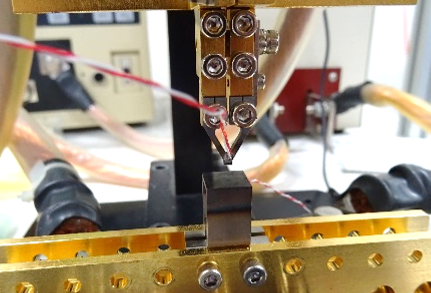
The pulse heat monitors the heating temperature so that only the required temperature is given to both the board side and the workpiece side, resulting in quality soldering.
Furthermore, the workpiece is held in place by the heater tip until the solder hardens, which prevents workpieces from out of alignment.
What is the pulse heat ?
Pulse Heat is our original welding method. Electric current is applied to a metal heating element called the heater chip, and soldering is performed instantaneously by heat and pressure using resistance heat generation.
The temperature of the heater tip is monitored from a thermocouple, and the workpiece is heated by applying set temperature to the heater tip. When the set heating time is over, the current is stopped to cool the workpiece, and when it reaches the set cooling temperature, the pressure is released.
This method is suitable for soldering precision components, which can ensure stability and reproducibility of soldering quality by precisely tracking of temperature profiles.
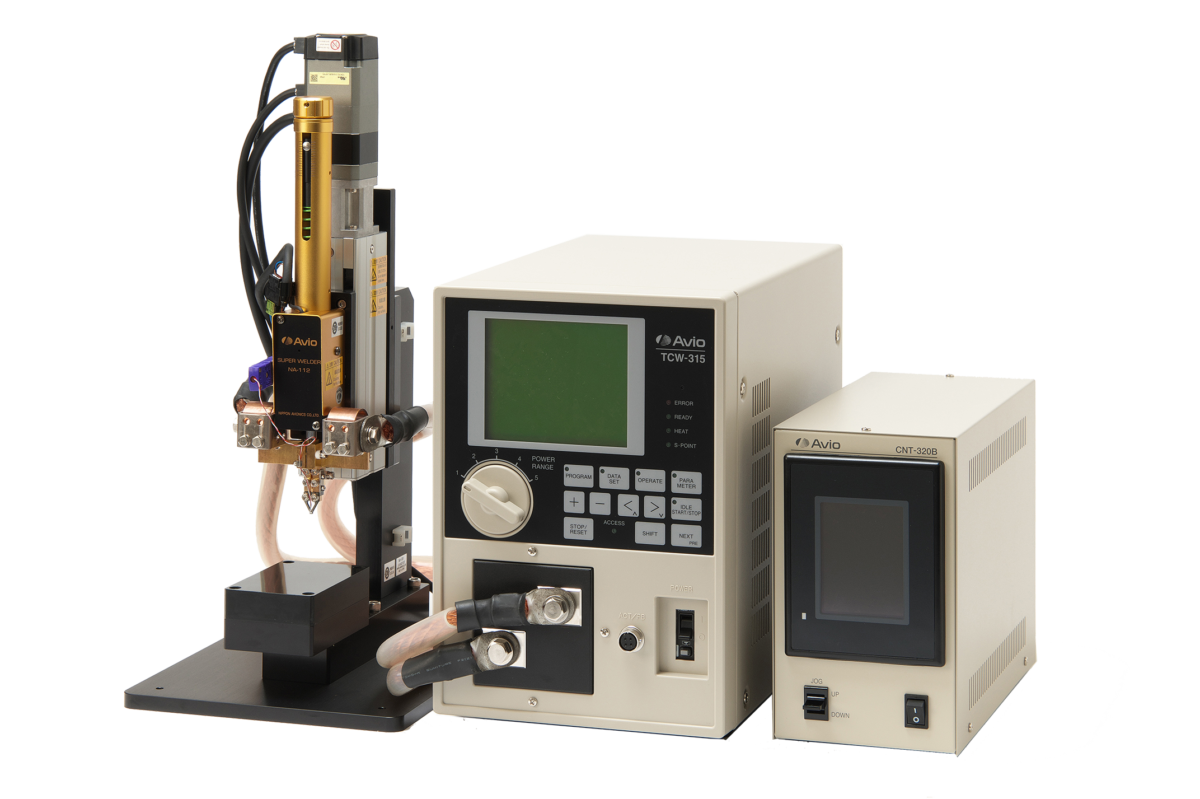
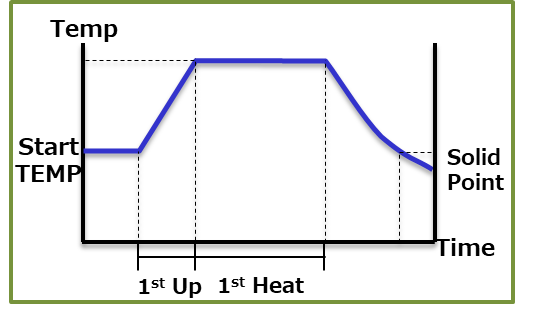
Click here for detailed principle of pulse heat.
Soldering of the high heat-dissipating board is possible by the pulse heat with top and bottom simultaneous heating!
The high heat-dissipating board such as ceramic, aluminum, and copper are difficult to solder because the nature of the board makes it difficult to melt solder.
The pulse heat, which enables instantaneous heating and cooling, heats the solder from both the workpiece side and the board side, making it easier to melt the solder, and the heater tip holds it down until the solder hardens to achieve good soldering with no workpiece misalignment.
For detailed specifications of the pulse heat unit, see this page.
Sample test
We will be pleased to test your sample with our proposed joining method and return it with a report.