What is fusing of magnet wire?
- TOP
- Resistance Welding
- Applications of Resistance Welding
- What is fusing of magnet wire?
Magnet wire is used for motor coils and other applications.
Fusing is a method of thermo-compression bonding (diffusion bonding) that uses resistance welding to connect terminals without removing coating of the magnet wire by solvent or other means in advance. It is also called “heat staking”.
In this article, the benefits of fusing, the joining principle, and the functions required of resistance welders for fusing, are explained.
Challenges for welding magnet wire and terminal
Magnet wires (winding wire) used for motor coils, etc., are generally covered with a coating such as enamel for insulation.
Conventionally, the coating material on the end of the magnet wire is peeled off, and then the wire is inserted into the terminal and caulked or soldered to the terminal.
Challenges for caulking and soldering are
In case chemically stripping with a stripper
- Capillary action may allow the stripper to penetrate into the winding, causing motor failure.
- Strict control is required for storage and handling of chemicals.
In case of soldering
- Coatings with higher heat resistance indexes are subject to copper corrosion and shorter solder bath life.
Fusing is a solution to this challenge!
Merit of fusing
Fusing is a process that welds the magnet wire and terminals and removes coating of the magnet wire simultaneously by applying electric current and pressure.
Fusing is very easy because the welding equipment automatically performs the process with predetermined joining conditions such as pressure, applying electric current, and crushing amount.
Fusing has the advantage of reducing the number of processes as well as failures, other than the cost at the time of machine installation.
Welding theory of fusing
The first current (pre-weld) burns the coating to ensure electric continuity, and the second current (main weld) joins the work.
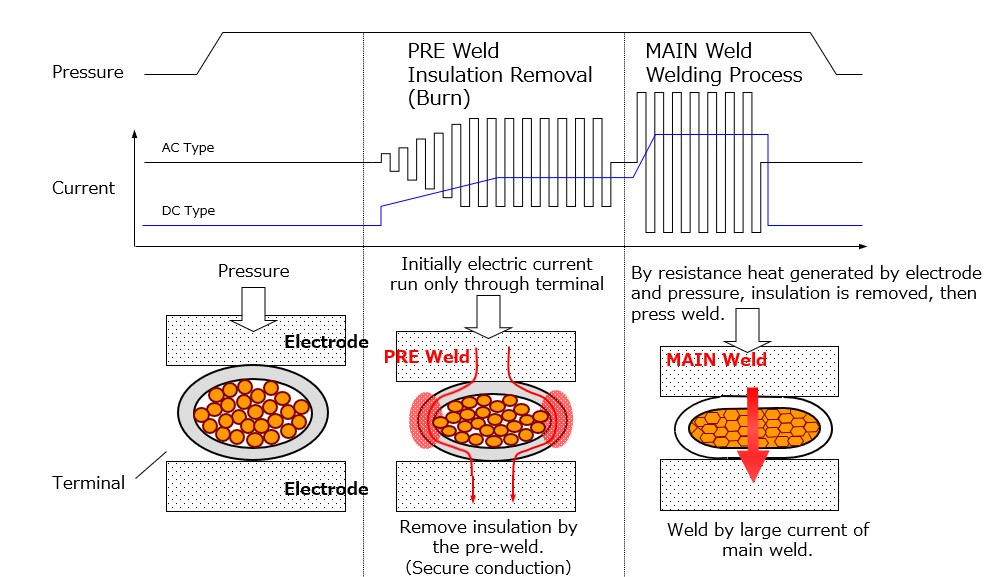
Functions required of resistance welder for fusing
The required functions of the resistance welding power supply and welding head for fusing are as follows.
Functions required for welding power supply
- Long-time welding (200ms or more or 10 cycles or more)
- Up-slope setting
- Multi-stage welding (2 or more stages are desirable)
- Multi-parameters (31 or more parameters are desirable)
Functions required for welding head (pressure unit)
- Smooth pressurizing operation
- Adequate cooling mechanism
- Pressure monitoring by load cell sensor
- Dimensional monitoring by displacement sensor
Recommended welding power supply for fusing NRW-IN400PA
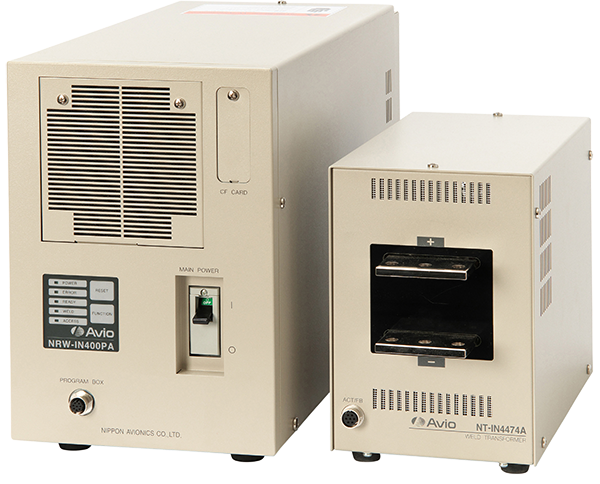
The NRW-IN400PA inverter-type welding power supply is equipped with the required functions for fusing.
Continent fusing is achieved.
3-stage welding function
Max. 3 phases with UP and DOWN slopes
Freestyle profile function (arbitrary waveform function)
Existing pulsation function, which sets the welding time and output, has been further evolved.
Combination of “UP”, “WELD”, “DOWN”, and “COOL” can be set as predetermined by user within a maximum of 127 steps (Free Style Profile).
Multi-stage slope welding, multi-stage welding, and arbitrary waveform pulsation are available.
Even in fusing where the heat balance between terminals and coils is not good (for example, a thick coil and thin terminals), the optimum heat setting can be made without thermally cutting the terminal.
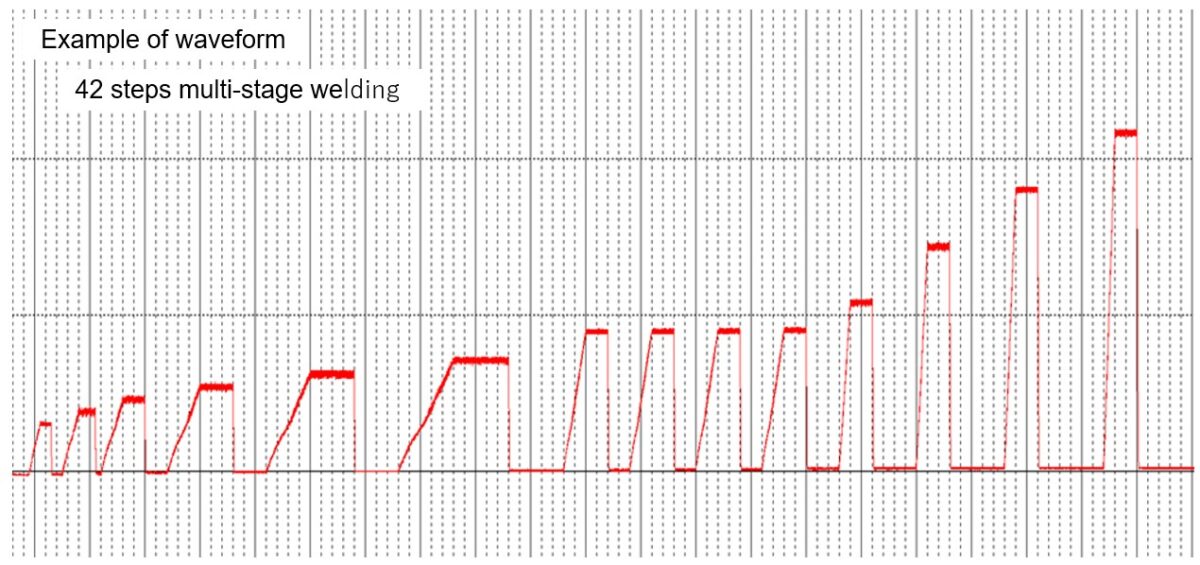
High-speed processing from the weld-stop command
Weld-stop commands from sensors such as displacement and load cells are processed at high speed. Weld stop is within 1ms to reduce finish variation and achieve consistent fusing.
Click here for details of inverter type resistance welder NRW-IN400PA
Fusing method is recommended for joining magnet wire terminals
Nippon Avionics support customers for technical consultation of fusing.
Fusing is a solution for challenges of connecting magnet wires to terminals by caulking or soldering.
Certain functions are required for resistance welders that performs fusing.
In order to achieve consistent fusing performance of resistance welder as well as know-how of resistance welding are the key.
Related video
Please be careful about the volume adjustment as this movie contains sound.
We are support customers for technical consultation of fusing
Nippon Avionics support customers for technical consultation of fusing.
Please feel free to contact us if you are interested in testing the actual joining condition.