How to fix the battery module and flexible printed circuit board (FPC)
- TOP
- Pulse Heat (Hot Bar Reflow) Soldering
- Applications of Pulse Heat (Hot Bar Reflow) Soldering
- How to fix the battery module and flexible printed circuit board (FPC)
In order for EVs to become popular, it is essential to increase their driving range. Therefore, it is necessary to reduce the weight of vehicle bodies and improve the performance of battery cells.
As the number of battery cells increases to extend the mileage and weight of the battery packs become heavier, there is a demand for reducing the weight of the battery pack.
In addition, lithium-ion batteries require a battery management system (BMS) to prevent smoking and combustion.
To monitor the voltage of each cell, the battery module and battery management unit (BMU) are connected using electrical wires.
Therefore, as the number of cells increases, the weight of the system increases due to the additional cables. Also, having more cables increases the risk of misconnections due to the higher number of connection points.
In order to reduce weight and eliminate incorrect wiring, the use of FPCs (flexible printed circuit boards) has begun to replace cable wiring.
In this case study, we will explain the advantages of fixing FPCs by using resin caulking using the Pulse Heat instead of using conventional metal frames and screws.
What is FPC?
FPC is an abbreviation for Flexible Printed Circuits, which means flexible printed circuit board.
An electric circuit is formed on a sheet made by laminating a soft, insulating thin film such as polyimide and a conductive metal such as copper foil.
It is a thin and lightweight board that is flexible and bends like paper.
It is mainly used in information terminals such as mobile phones and electronic devices such as digital cameras, as well as connectors.
Benefits of replacing wiring from cable to FPC
Replacing cable wiring with FPC can save space and reduce the work of connecting cables.
FPCs are thin and bendable, making them suitable for connection in tight spaces and at curved sections. This increases the degree of freedom in wiring design.
Additionally, cable wiring is prone to quality variations and incorrect wiring. FPC produces better finishes with fewer wiring errors, and with consistent manufacturing quality.
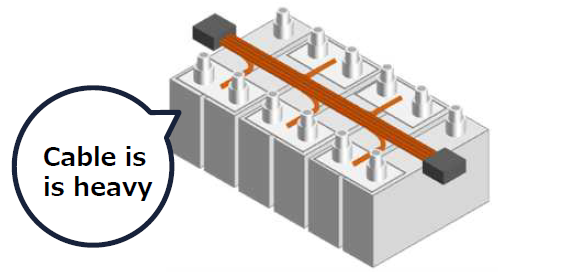
The challenge is how to fix the FPC.
Fixing it with screws or a metal frame would increase the weight. An effective way to solve this problem is to use resin caulking to reduce the weight.
Features of the Pulse Heat
Pulse heat is Avio‘s proprietary method of passing an electric current through a metal heating element called a heater tip/heater tool, which is equivalent to a soldering iron, and using resistance heating to instantly perform soldering, thermocompression bonding, and resin welding using heat and pressure.
The temperature of the heater tip/heater tool is measured by a thermocouple, providing feedback to replicate the set temperature profile.
- It has quick temperature ramp up and good temperature reproducibility.
- Temperature profiles such as pre/main heat can be easily realized.
- Because it is local heating, there is minimal heat impact on the surrounding areas.
- Since it cools while being pressed down, there are no loose connections due to floating.
- It is not influenced by the skill level of the worker.
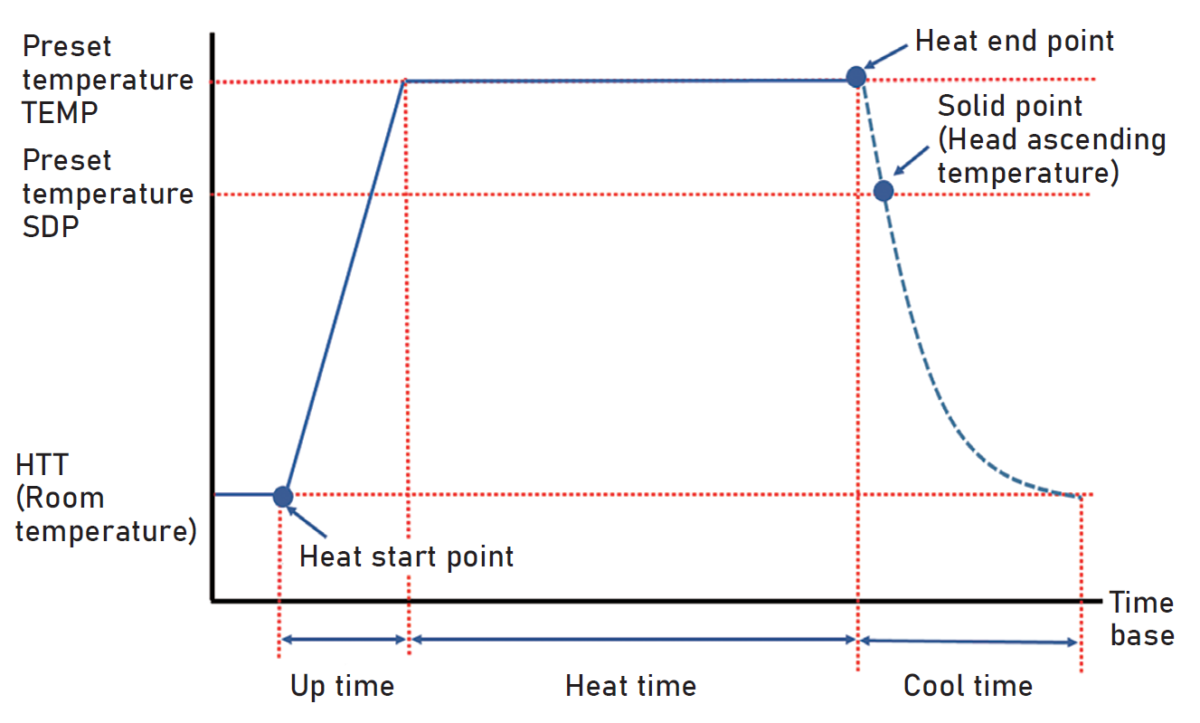
Benefits of heat caulking with the Pulse Heat
Pulse heat allows you to monitor the temperature and melt the resin at a set temperature.
Since the temperature is controlled, it achieves more consistent resin caulking compared to constant heating methods.
In addition, because the heating is localized, the thermal impact on the surrounding area can be reduced.
- Consistent and repeatable resin caulking is achieved.
- Because it is instantaneous heating method, heat is generated only when electric current is passed through and stopped when turned off that prevents stringiness.
- By holding down the resin until it hardens, a beautiful exterior finish is realized.
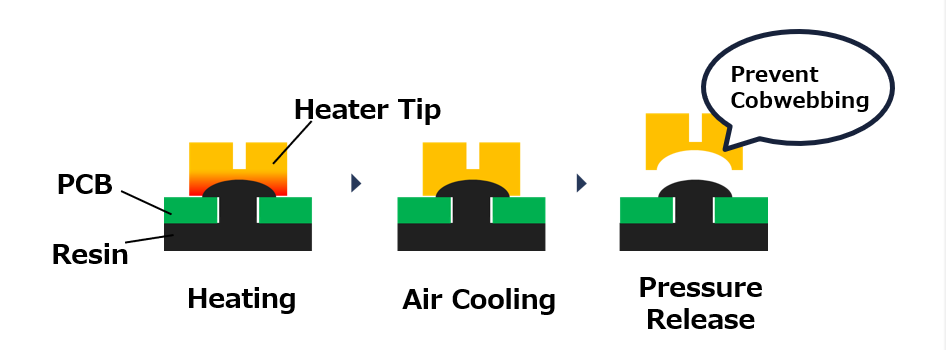
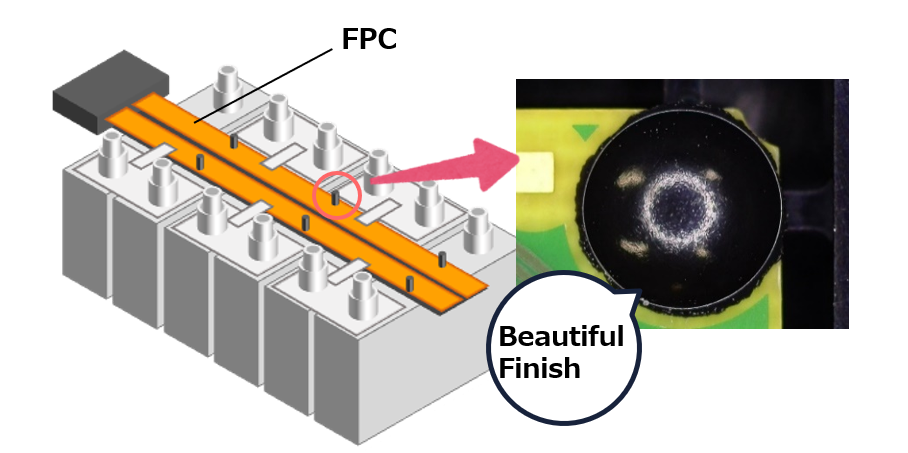
In battery modules for electric vehicles, the connection of the battery management unit (BMU) is being replaced from conventional cable wiring to FPC wiring in order to reduce weight.
When fixing FPC, using resin is suitable for reducing weight. The fixing method is `heat caulking'', which melts the resin with heat.
However, if you use the constant heating method, there is a risk of resin stringiness and potential heat impact on surrounding components.
Pulse heat is an instantaneous heating method that allows temperature control.
This makes it possible to heat caulk with a beautiful appearance without stringiness, and also to minimize the effect of heat on the surrounding area
If you are in need of fixing FPCs, please contact Nippon Avionics, a company that specializes in heat caulking by the pulse heat.
Sample test
We will be pleased to test your sample with our proposed joining method and return it with a report.